Industry is undergoing a major digital transition. Production lines are becoming automated, industrial robots are used in many stages of manufacturing, and a number of manual tasks are now completed digitally. One of the technologies that is transforming the field is industrial additive manufacturing (AM) – more commonly known as industrial 3D printing. It can improve the performance, efficiency and functionality of products in a range of industry sectors. In some cases, industrial 3D printing is even applied to mass production.
According to Heidi Piili, doctoral candidate at LUT University, especially the additive manufacturing of metals has significant potential globally. The number of industrial AM systems for metals is growing steadily also in Finland.
The possibilities provided by additive manufacturing steer production towards sustainability.
“The additive manufacturing of metals is expected to keep increasing in the coming years, and the chemical industry could be one of the sectors that will gain the greatest benefits. Automated design algorithms will be able to solve product design challenges of complex parts already in the near future,” says Piili, who is currently working as an adjunct professor of mechanical engineering at the University of Turku.
The industrial additive manufacturing of metal parts and structures accelerates product development and manufacturing, which in turn reduces the costs of a variety of products. Moreover, the method enables the manufacture of increasingly complex products and detailed designs of functional structures that can improve the energy efficiency of products and reduce waste more effectively than conventional fabrication methods.
“The possibilities provided by additive manufacturing steer production towards sustainability. Resource efficiency and production near the end-user can significantly reduce environmental impacts.”
What does 3D printing mean?
- 3D printing means creating a three-dimensional object by adding one layer of material at a time. The industrial term is additive manufacturing (AM) or industrial 3D printing, and it is part of the digitalization of industry.
- The most common materials used in industrial additive manufacturing are plastics and metals. Ceramic and multimaterial 3D printing, for example, is also possible.
- For instance, the automotive, aviation and pharmaceutical industries apply industrial 3D printing, and mechanical and electrical engineering applications are on the rise as well. Moreover, additive manufacturing applications will spread to other industry sectors in the future.
- The limited availability of industrial AM systems, patent protection periods and immature information technology have previously impeded the spread of additive manufacturing, but in the past ten years, the field has advanced substantially.
- The future of industrial 3D printing involves responding to quality-related challenges and developing a comprehensive approach that uses artificial intelligence algorithms to integrate automated design tools with simulation-aided optimization and real-time monitoring of the printing process.
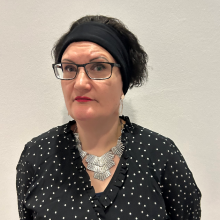
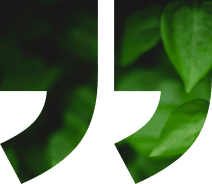
Solution to problems of industrial 3D printing of metals
The industrial 3D printing technology for metals is revolutionary but still has its limitations and constraints, as does any other manufacturing technology. For example, parts done by industrial 3D metal printing require support structures if the product has angles of under 45 degrees. The support ensures that each layer of material adheres correctly to the layer underneath. However, support structures pose problems of their own.
“Support structures add to the complexity of the printed part and the manufacturing process. Adding support requires additional planning, which means more work and delays. These structures also need to be removed at the end in order to finalize the product. All that adds to the costs,” Heidi Piili describes.
Piili has studied how the current constraints of product design could be overcome. In her doctoral dissertation, she proposes a new way of incorporating automated, modern product design tools into simulation and the real-time monitoring of the printing process.
Optimized components improve the efficiency, sustainability and quality of systems considerably.
“The solution enables the manufacturing of parts without support structures, minimizing heat distortion and guaranteeing quality even at zero-degree building angles. With AI algorithms, the programme can determine beforehand how to manufacture challenging shapes and solve fabrication problems.”
Unlike applications currently on the market, Piili’s approach calculates the manufacturing strategy of the printout ahead of time.
“When challenging sections are identified before manufacture, it’s faster to analyse the quality of the problems and offer a finite number of solutions. As a result, real-time decisions become easier and quicker to make.”
Examples of what industrial 3D printing could create for the chemical industry
- Components for hydrogen production and storage
- Fuel cells for electricity production
- Components for greenhouse gas filtration
- Tailored water filtration units for when conventional water purification devices are not readily available
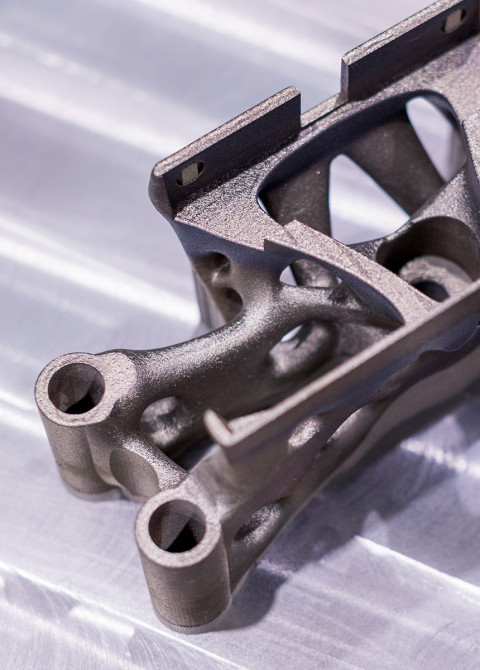
The chemical industry could exploit industrial 3D printing more extensively
Piili’s dissertation focuses on the industrial 3D printing of metals in the chemical industry, such as in separation and purification technology applications. According to Piili, advanced computation tools, simulation and methods could be put to wider use in product design.
“Optimized components improve the efficiency, sustainability and quality of systems considerably,” she explains.
Piili estimates that the chemical industry in Finland or even internationally has not yet tapped into the full potential of industrial 3D printing. Conventional manufacturing methods, such as forming and machining, are frequently applied in the global chemical industry.
“Chemical industry actors are cautions about adopting new manufacturing technologies. One obstacle is the prevailing notion of industrial 3D printing being slow and its initial costs being high. It’s easy to forget that there's rarely a need to print entire products – the most critical component may suffice. It can then be attached to the larger construction by means such as welding.”
More information:
Heidi Piili
doctoral candidate (LUT University)
adjunct professor, mechanical engineering
(University of Turku)
heidi.piili@utu.fi
+358 50 473 4723
Heidi Piili, Doctor of Science (Technology), will defend her doctoral dissertation in the field of Chemical Engineering at LUT on 14th of December 2023 in auditorium AUD3B in Lahti and online.
Her dissertation is titled "A conceptual, holistic framework to overcome limitations and constraints of design in laser based powder bed fusion of metals: Case novel separation and purification units".