Around 100 million passenger vehicles and 20 million heavy vehicles are manufactured in the world each year. The electrification of vehicles is now progressing at a fast pace, and concern for the earth's resources has become obvious. Car motor manufacturers themselves have begun to develop resource-efficient motors, but now the authorities have also begun to demand more and more energy- and material efficient motors.
In commercial vehicles, generation after generation, motor speeds have increased. Current motors spin at a maximum of almost 20,000 rpm. The majority of them are permanent magnet synchronous motors consuming lots of rare earth materials. An electric motor - especially a motor using permanent magnets - can practically be built to be very energy efficient.
However, EU and US authorities want the electric motors of electric cars to be as material-efficient and inexpensive as possible. The use of rare earth metals (e.g. Neodymium and Dysprosium) should be strongly restricted. To achieve such goals, a high-speed motor is needed. The mass of permanent magnets in motors should be reduced or their use stopped. The advantage of the induction machine and the synchronous machine is that permanent magnets are not needed at all. However, in terms of efficiency, a permanent magnet synchronous machine is often unbeatable.
Research projects are currently underway in the EU, where the goals set for the electric motor are: Specific power 7 kW/kg, power density 23 kW/liter, cost less than €6/kW and the use of permanent magnet materials based on rare earth metals at least 60% lower than in current car motors. Despite the scarcity of resources, the motor should have high efficiency.
For example, a motor with a continuous power of 120 kW and a peak power of 200 kW can only have a total mass of 17.1 kg and a total volume of 5.2 liters. For example, the motor of the Tesla Model 3 has 1.8 kg of neodymium iron boron magnets. Thus, in the EU project, the permitted mass of NdFeB magnets would be a maximum of approximately 700 g per motor. With such restrictions, the cost target can be reached, but the efficiency of the motor is easily lower than in the current power lines of top-class electric cars. Automotive permanent magnet synchronous machines that use plenty of magnets can reach 96% efficiency at their best operating point, and the high efficiency is maintained over a very wide operating range.
A high-speed (12000 rpm nominal speed and 30000 rpm max.) motor developed with the above-mentioned boundary conditions can achieve almost 95% efficiency at its best operating point. The high efficiency of the motor is extensive and offers at least 94% efficiency at the practical operating points of the motor, as shown in Figure 1.
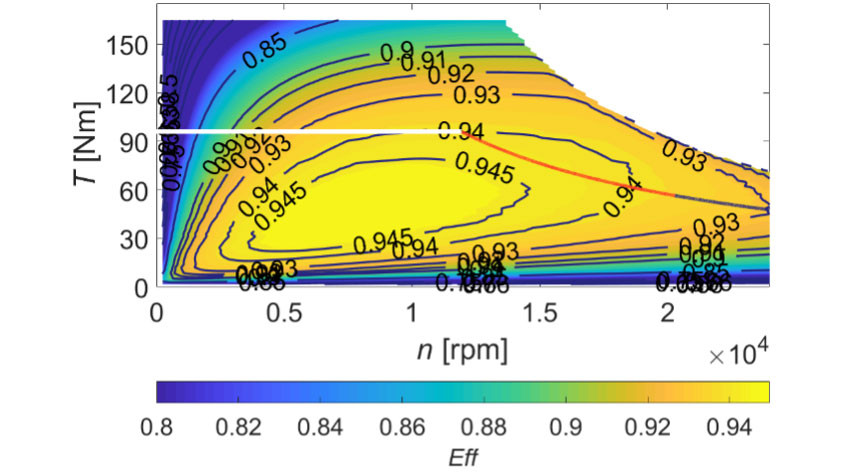
Members of the LUT Inercom research platform from the electrical drives technology and machine dynamics laboratory have been working on this motor development since last spring winter. The goal is very challenging when the electromagnetic, thermal and mechanical stresses of the motor are taken to the extreme. However, we already have several versions that meet most of the EU requirements, but there is still plenty to optimize.
The project involves partners from Sweden, Germany, Slovenia, Cyprus and Ukraine. The project is coordinated by VTT, but LUT's contribution to the new motor innovation is central. We have e.g. two patent applications that could significantly change the electric car motor of the future.