Research group of Steel Structures has been a trailblazer in the field of design and technical strength analysis of mechanical components in Finland since 1974. Recently, the performance of steel structures made of high-strength and ultra-high-strength steels has been the key area in the research and educational work. Steel Structures also is actively involved in the international communities, and the research group is well-known e.g., in the International Institute of Welding (IIW).
Steel Structures offers comprehensive research infrastructure for experimental and numerical studies:
Steel Structures unit provides an exceptional research environment for advanced mechanical testing and structural analysis. The facilities include state-of-the-art equipment for static and fatigue testing, with capacities up to 5000 kN, and high-frequency fatigue testing capabilities in the high-cycle regime (up to 160 Hz).
The unit also specializes in testing large-scale components with dedicated setups designed for complex and actual-size structures. Additionally, it offers advanced rigs with environment chambers for specialized testing under subzero conditions (-60°C).
Comprehensive material and component characterization equipment are available, including residual stress measurements, 3D geometry scanning, SEM analysis, and surface profiling. Finite element analysis is extensively utilized to evaluate structural behavior through stress analysis and to conduct advanced computational weld mechanics simulations, ensuring robust support for cutting-edge research and industry collaboration.
The main focus areas of research are:
- Static and fatigue strength of welded joints and cut edges
- Fatigue strength assessment methods
- Static and fatigue strength of welded joints and components
- Usability of high-strength steels and ultra-high-strength steels
- Structural performance and quality of high-strength steels
- Enhancement of fatigue strength of welded joints by welding techniques and post-weld treatments
- Numerical methods and analysis of welded structures, e.g. stress analysis and computational weld mechanics
Group members
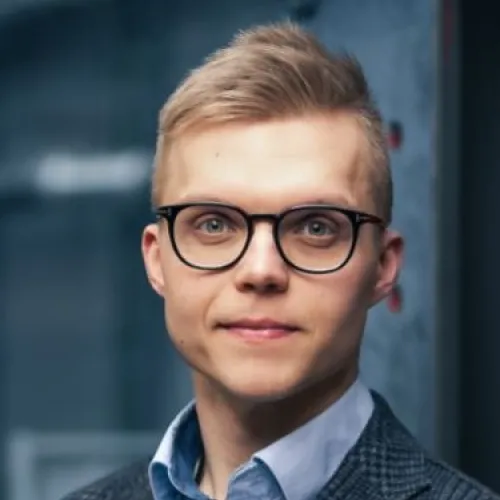
Antti Ahola
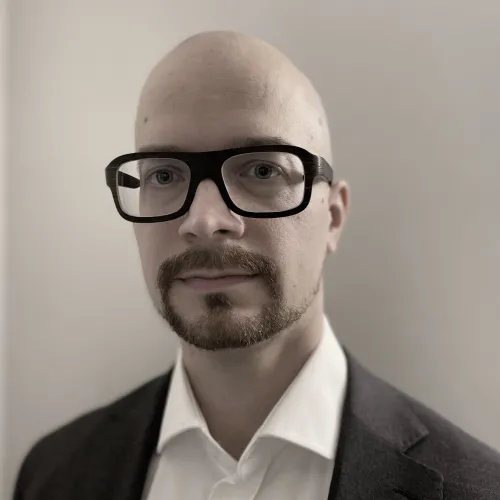
Tuomas Skriko
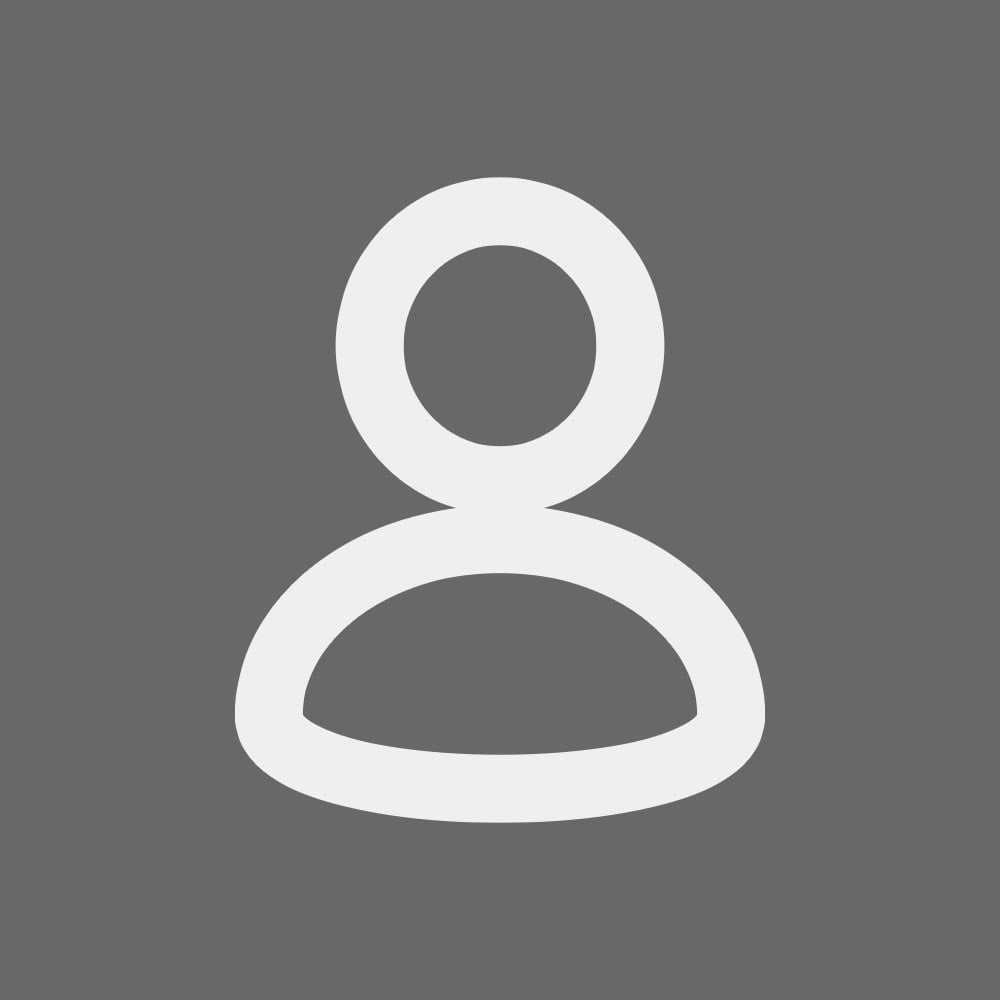
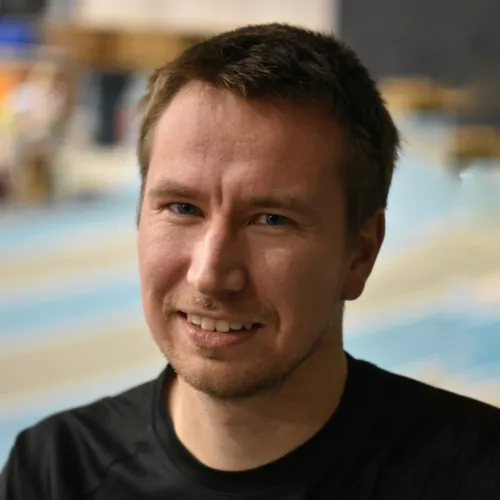
Kalle Lipiäinen
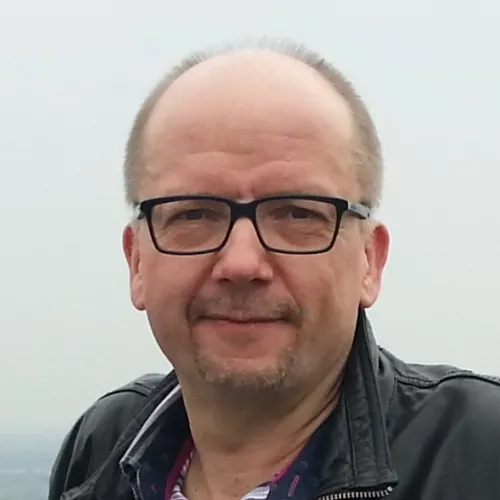
Matti Koskimäki
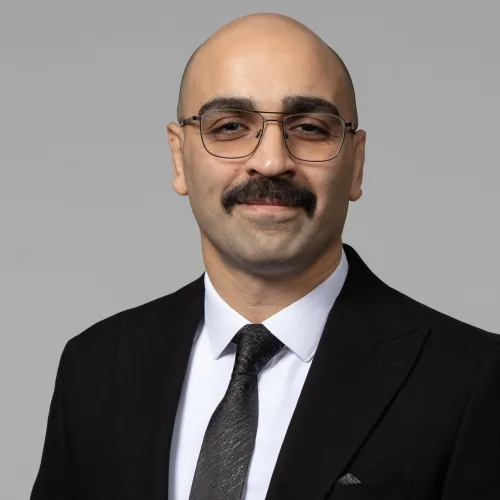
Hamidreza Rohani Raftar
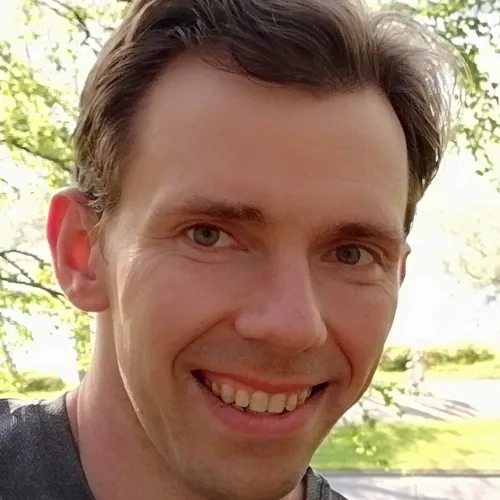
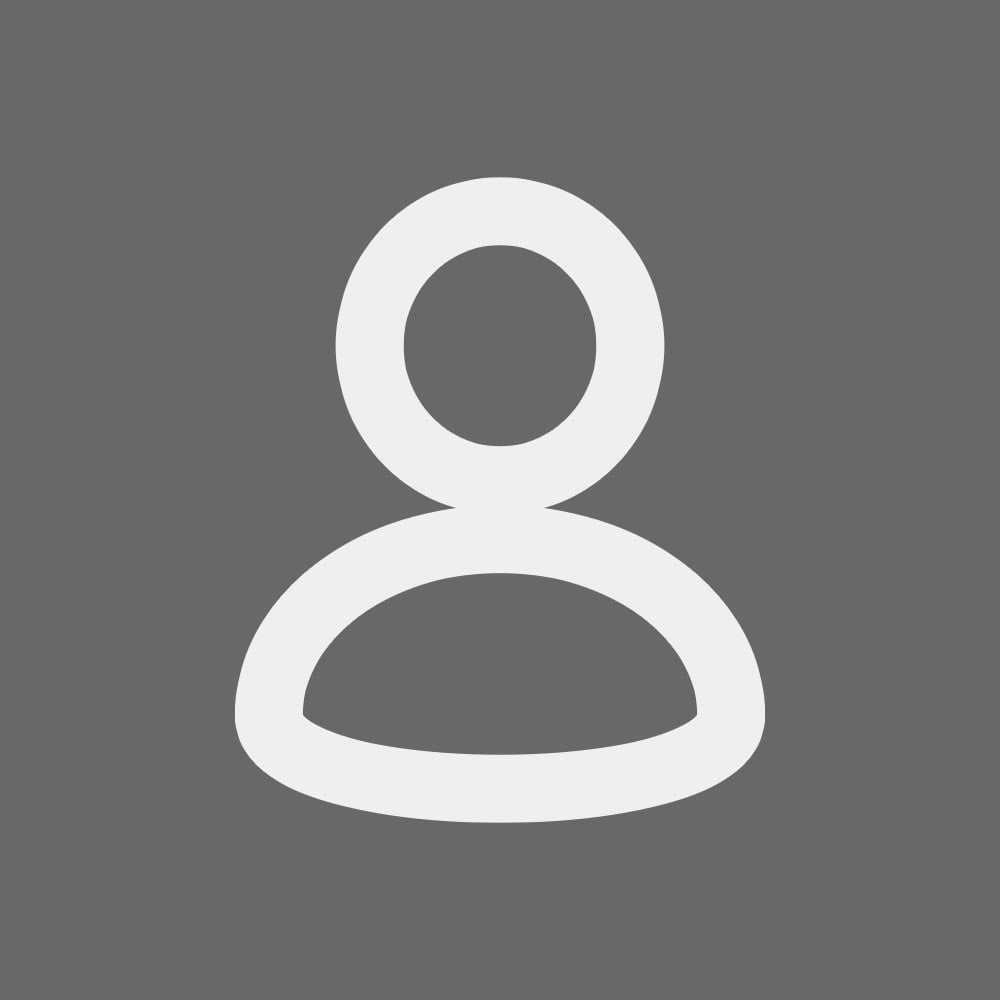
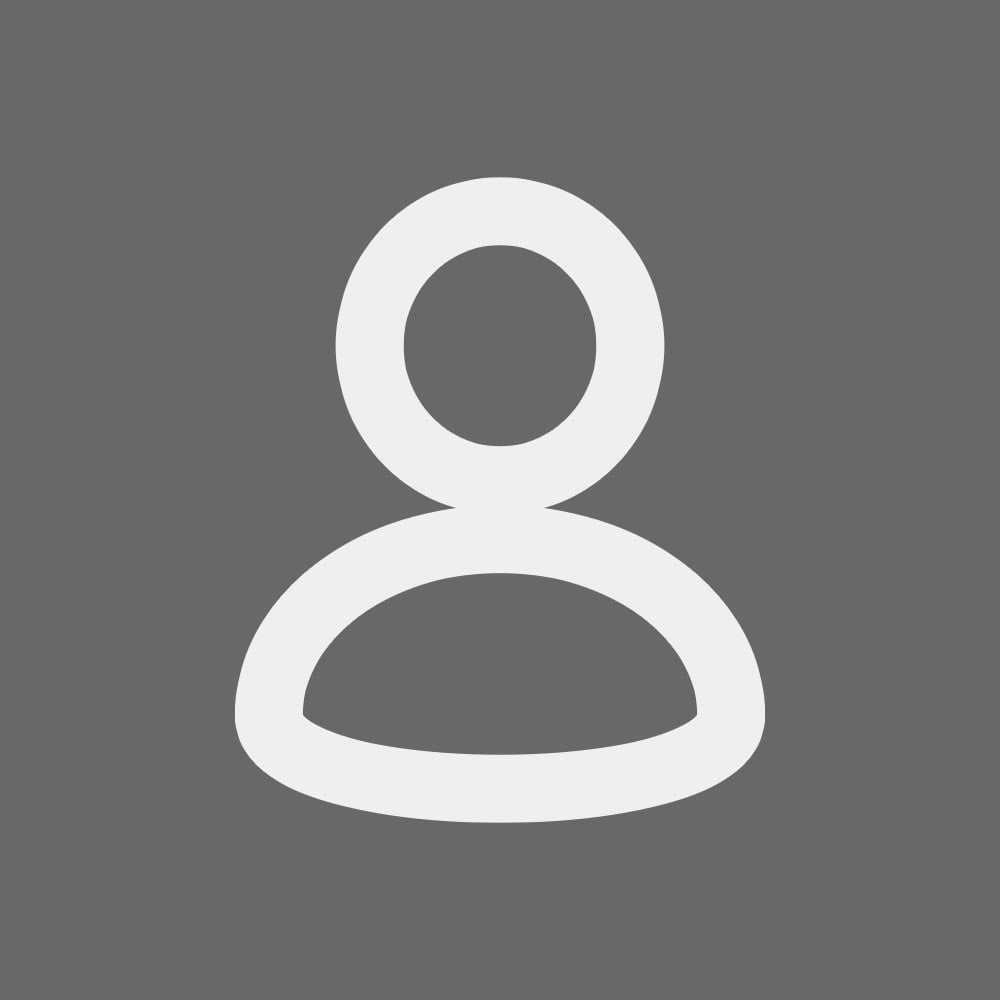
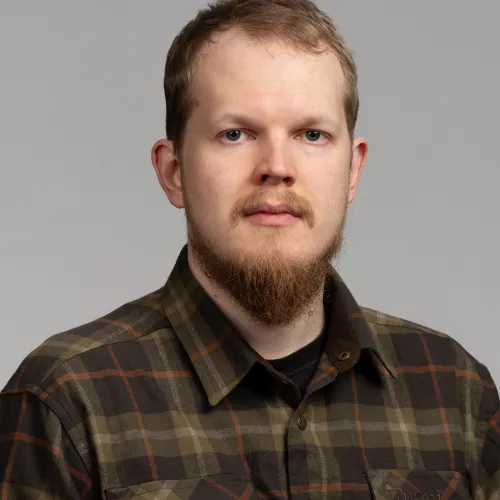
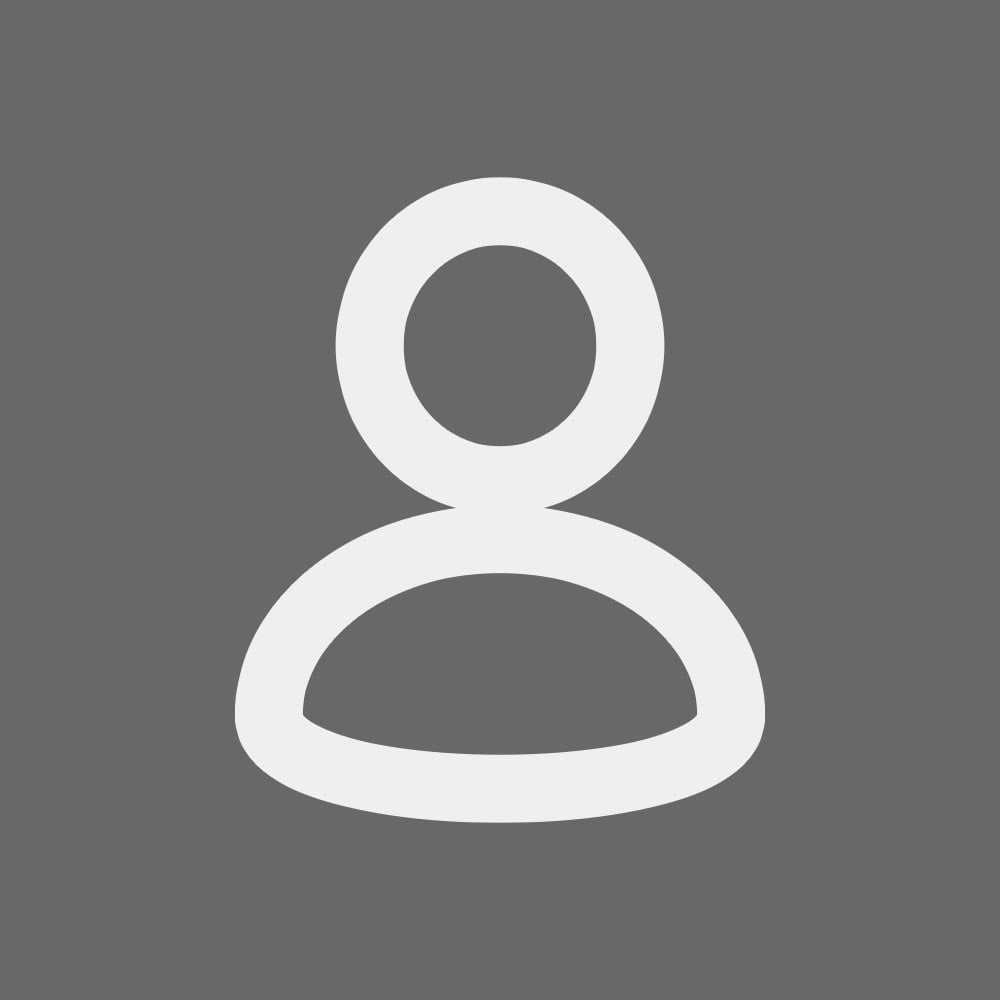
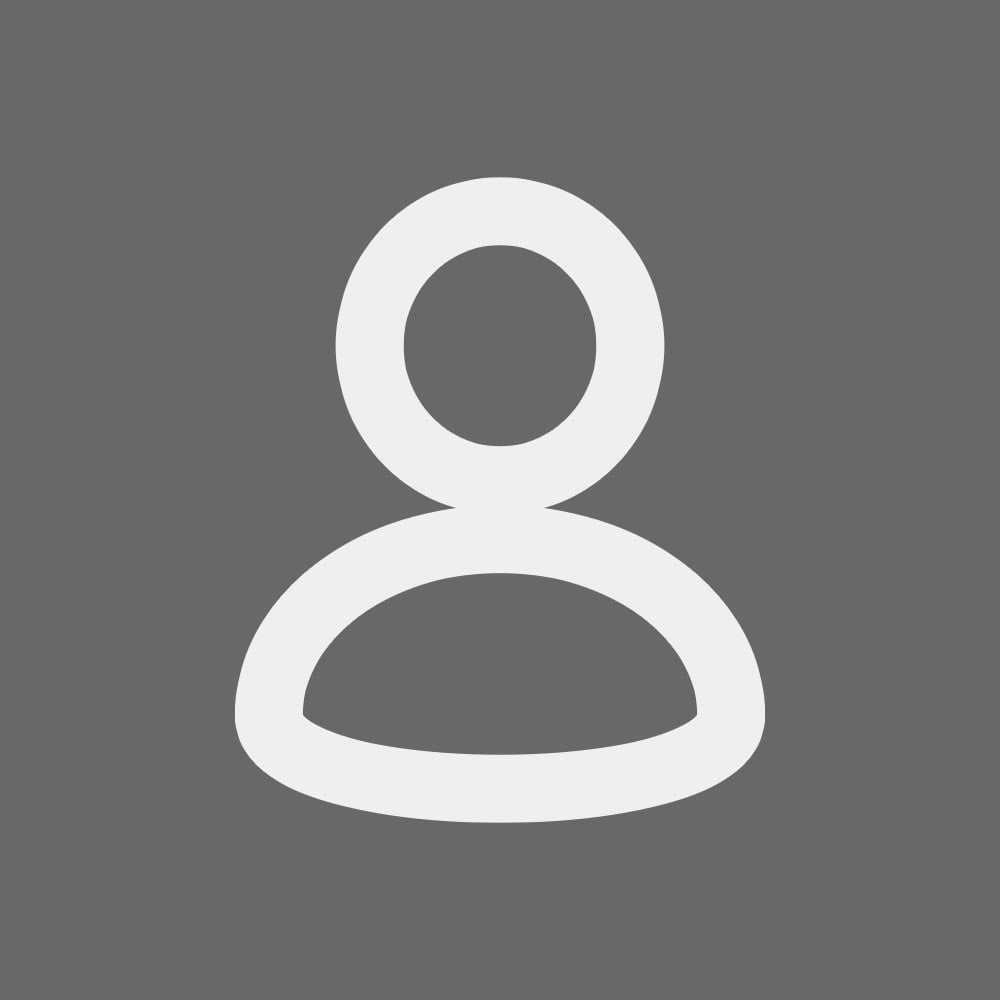