Brief desciption of the invention
The maximum coil current in the electromagnet used to actively control position of the levitated mass can be limited by the control methods that are not based on direct current control, such as direct flux control or force (and or moment) control or voltage control methods. The inclusion of the overcurrent protection into the control method will make the hardware overcurrent protection redundant in the same control system, a bandwidth of the non-direct current control method can be increased, and an estimation of control variables can be improved. This invention provides means to mitigate the current rise to unfeasible levels in the coils of the electromagnets by introducing an overcurrent protection into the control methods that are not based on the direct current control. The advantages of such solution include: redundancy of the hardware protection and better estimation of control variables by the control methods.
Magnetic levitation systems are well known in the art. The systems that require active control such as active magnetic bearing systems, linear movement systems or bearingless motors are commonly utilized for supporting of rotating or oscillating mass. For magnetic levitation systems the support of the mass at each axis or direction is obtained by balancing forces due to fluxes of electromagnets (and possibly of permanent magnets) and external loads.
The most typical control methods include direct current control. ln such a method the controller for each degree of freedom typically comprises an outer position control loop and an inner current control loop. The outer controller output is a reference current signal (or vector of signals) or control current signal (or vector of signals).
Magnetic bearing control methods that are not based on direct current control (where current is not controlled directly), such as but not limited to direct flux control or force (and or moment) control or voltage control methods or equivalent black-box model-based control methods, which have states without physical meaning, can result in the overcurrent during transient conditions. Such conditions can appear, for example, during an initial levitation of the rotor, when sudden external force act on the rotor or when new step reference position command is provided to the control system. The coils in the electromagnetic actuators of magnetic bearing rotor systems are designed and manufactured to be able to tolerate certain maximum current levels. The overcurrent appears when the coil current rises beyond that maximum level. Additionally, when current value stays close to the maximum value for long period of time it also may result in a temperature rise and electrical failure.
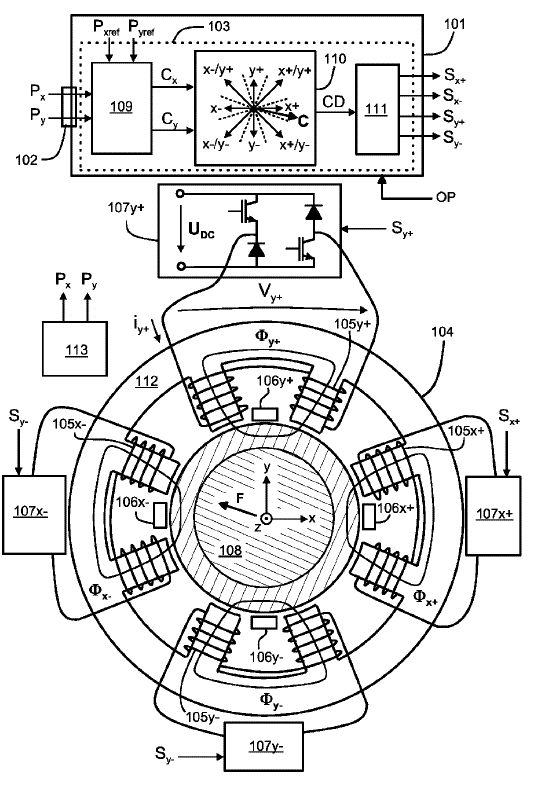
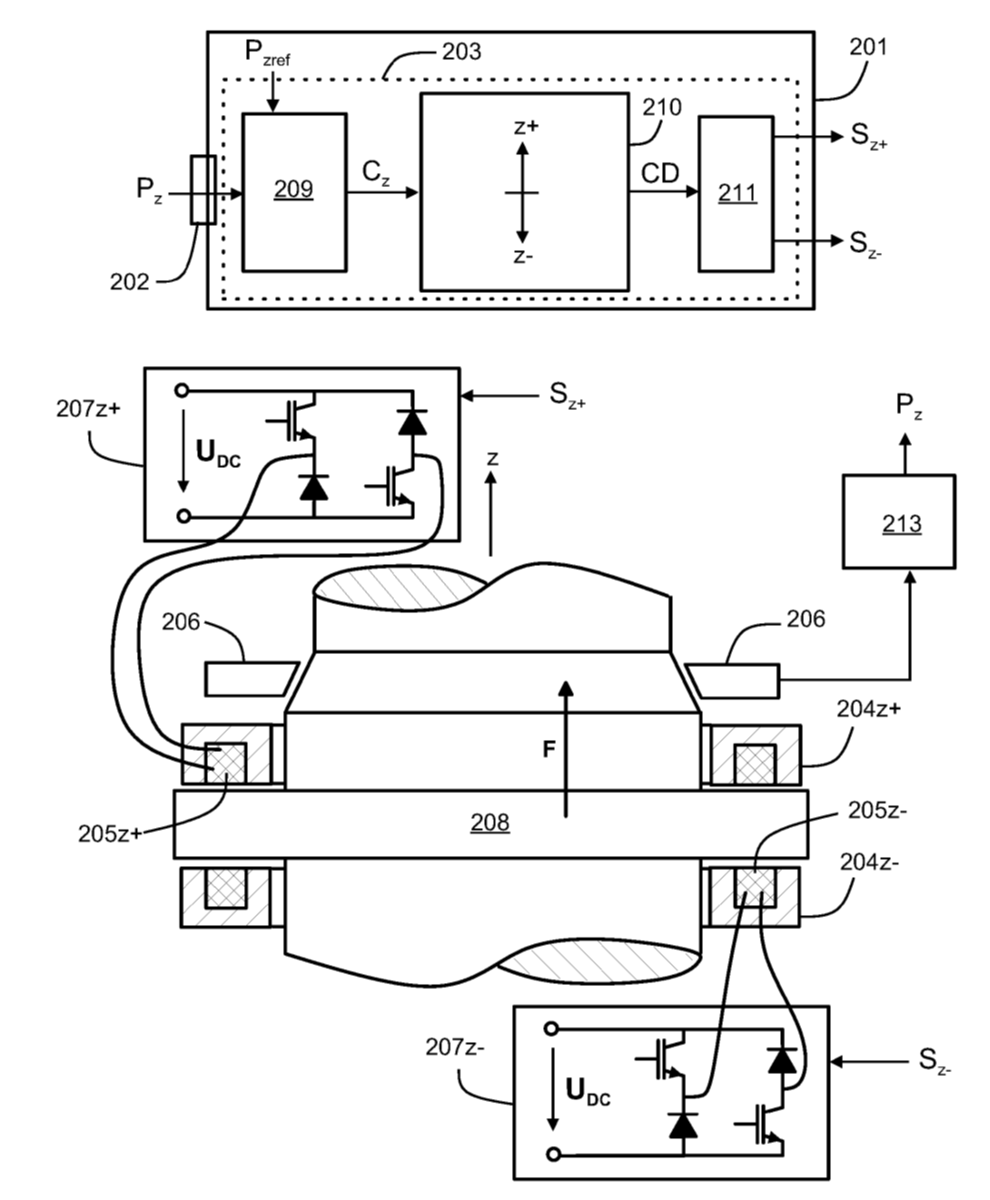
Liitteet
Lisää aiheesta
Ota yhteyttä
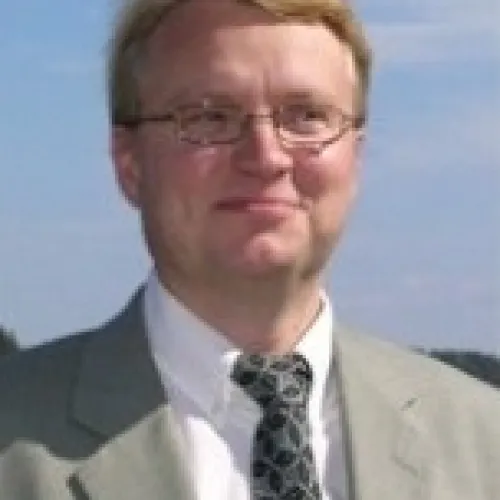
Tero Lehikoinen
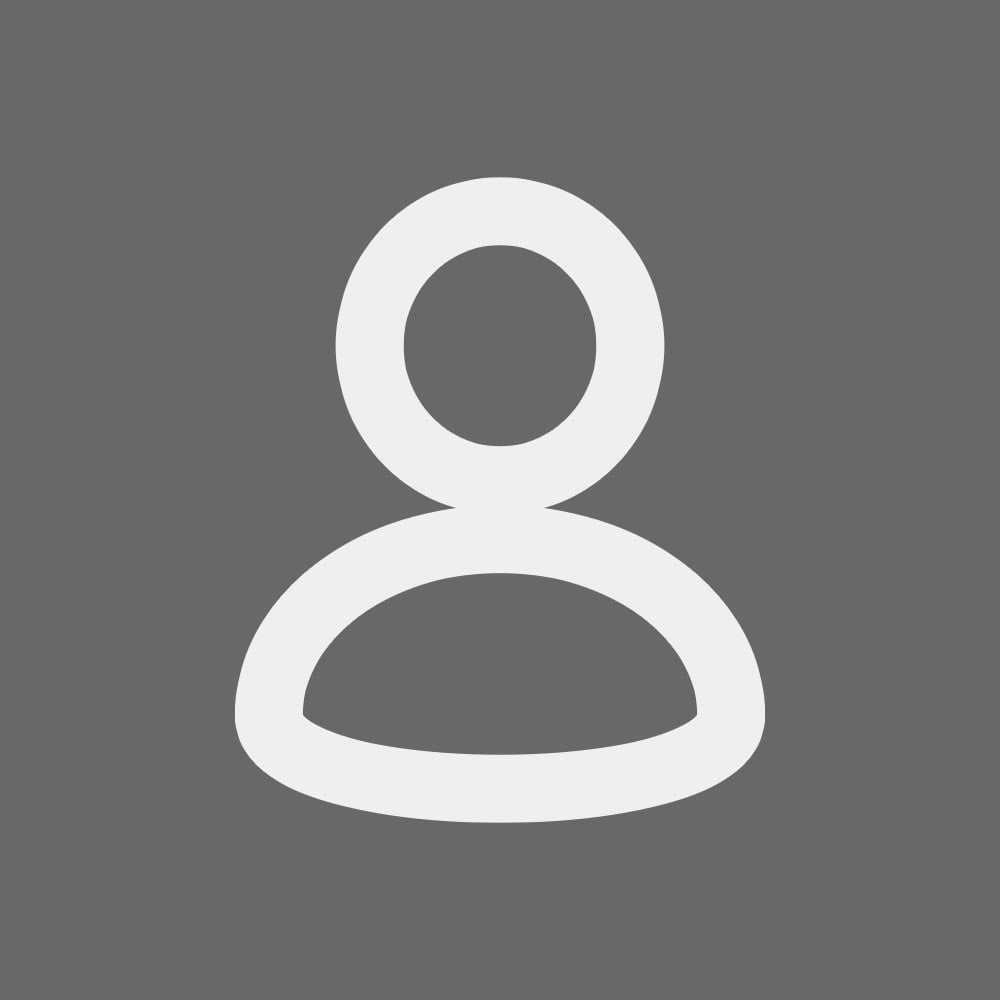